Compression Packed Valves
Elements
Key operated, single spindle, metal seated
Common valve body materials
Brass, Al-Si bronze
Description
These valves use compressed packing to make a seal around the valve spindle & body. To ensure a good seal, the packing nut is tightened to compress the packing against the spindle. As this results in higher torques, the valve is operated with wrench. The design allows for tightening of the gland nut in case of leakage past the packings.
Application
These valves are used for corrosive gases because of the ability of the operating mechanism to withstand higher torques to overcome any build-up of salts or contaminants in the seating area. They are generally used up to valve test pressure of 50 bar & not preferred for high purity applications because of particulate generation from valve seat & packing wear.
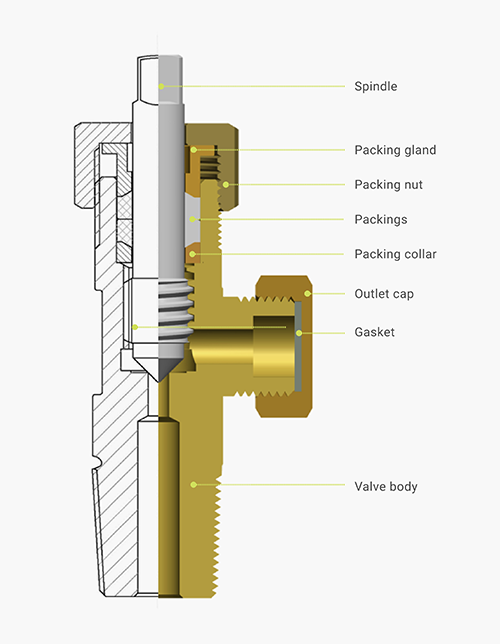
O-Ring Seal Valves
Elements
Two-piece spindle, soft seated, brass body
Description
These valves have a non-rising upper spindle & threaded lower spindle. It uses O-ring/s to create a seal around the upper spindle. The top spindle is designed to fail first, allowing valve maintenance & package content recovery in the event of a failure, even when the cylinder is full. These valves come in key, toggle, handwheel & handle operation.
Application
These valves are easier to operate than packed valves due to absence of packing load on the upper spindle & hence used for a wide range of pressure & non-corrosive gas applications where low torque operation is desired.
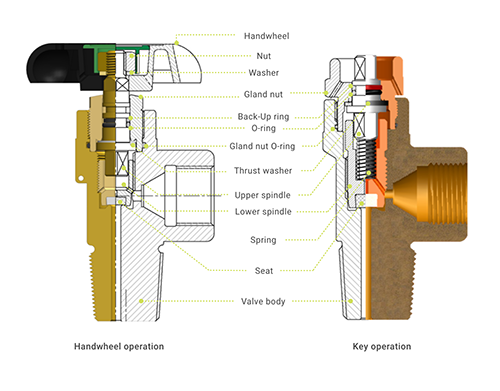
Diaphragm Seal Valves
Elements
Handwheel operated, two-piece spindle, soft seated
Common valve body materials
Stainless steel, Brass
Description
These valves use diaphragms for gland sealing which gives the valves superior leak integrity. The gland nut threads into the valve body & clamps the outer edges of the diaphragms against a ledge in the valve body to form a seal. The lower spindle assembly is non-threaded & non-lubricated, encased in a spring which forces it away from the seat when the valve is opened. The upper spindle is threaded into the gland nut. The valve opening is restricted by the stroke of the diaphragm, limiting the flow through the valve.
Application
The design is highly suitable for toxic, pyrophoric & high purity gas. Due to high torque required to close the valve by overcoming cylinder pressure X area of the diaphragm plus the spring force, the use of these valves is limited to cylinder pressure up to 200 bar.
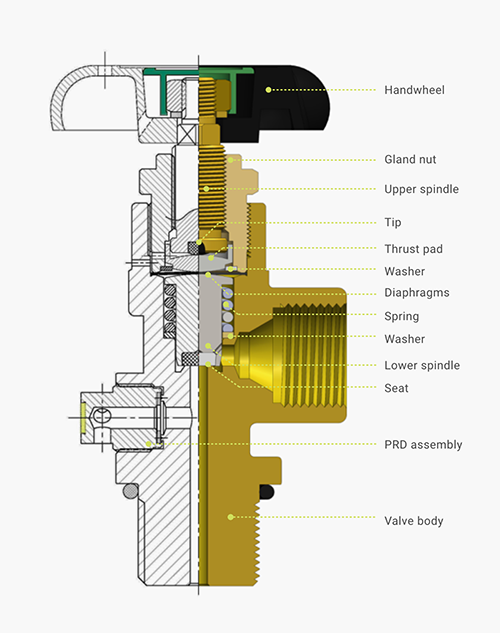
Compression Packed Valves with O-ring Seal Technology
Elements
Handwheel operated, two-piece spindle, soft seated
Common valve body materials
Brass, Al-Si Bronze, Carbon Steel & Stainless Steel
Description
These valves combine compressed gland packing & O-ring technology to gland seal the valve. The lower spindle connects to the upper spindle via a slip joint. The lower spindle assembly seals against the seat without rotating, reducing wear & particle generation. The gland nut is usually secured by a lock nut having threads in the opposite direction to prevent accidental loosening of the gland nut.
Application
Unlike the single spindle packed valve, the packing is smaller, better contained, spring loaded & backed by O-ring/s. This allows the mechanism to seal with handwheel up to 200 bar & eliminates the need to retighten gland nut making the design very suitable for toxic & corrosive gases.
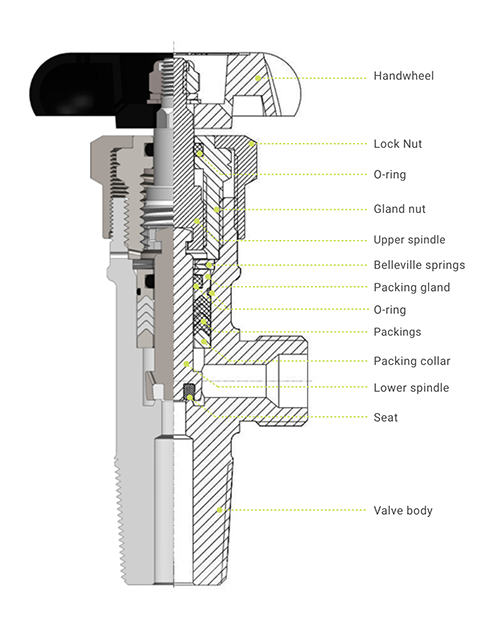
Residual Pressure Valves (RPVs)
Description
These valves are fitted with an offline or inline Residual Pressure Device (RPD). The RPD usually has a built in Non-Return Valve (NRV) function to prevent backflow of downstream contents preventing contamination risks as a result of positive pressure always present in the cylinder. RPV technology provides improved safety of the cylinder & ensures purity of gas contents negating the need to purge cylinder each time it comes back for filling. The user needs a filling connector consisting of a projected “Pin” during filling & evacuation to neutralize the NRV function.
Offline RPV
The outlet is offset with respect to the inlet plane & the RPD is backside of the outlet. Offline valves can be designed for any outlet connection but are mainly used for outlet with internal threads & for external threaded outlet requiring sealing in the cone. They are less restrictive on the flow passage of the valve.
Inline RPV
The RPD is contained within the outlet & therefore is mainly used for external threaded outlet requiring sealing on the face. Due to limitation of the volume within which the inline RPD has to be accommodated, they have greater flow limitation than the offline version.
Application
RPVs are highly recommended for:
1. Carbon steel cylinder applications where there is a possibility of internal corrosion due to ingress of fluid.
2. Applications where gas purity is important,
3. Gases & gas mixtures which are susceptible to stress corrosion cracking
4. Applications where the possibility of back flow contamination from the end users process can create hazardous conditions,
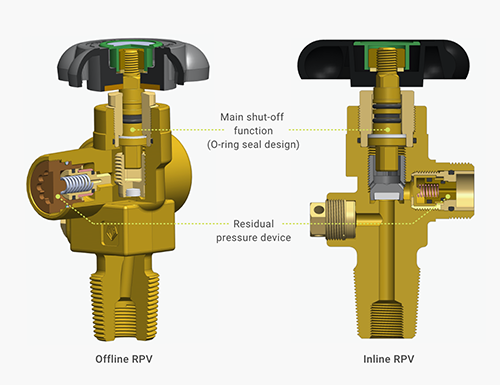
Reverse Seated Valves
Elements
Lever type (squeeze grip), single spindle, soft seated, brass body
Description
These valves use an O-ring to seal around the valve spindle. Pressure tends to keep the valve shut & as the cylinder pressure decreases, the total force available to sustain valve shut-off also decreases & seat closure is achieved by spring force. If there is a leak at the seat when the valve closes, there is no way to manually apply more force.
Application
This design is used for carbon dioxide valves for firefighting application where quick release of gas content is desired.
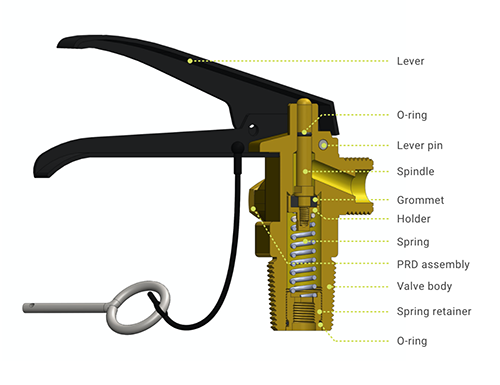